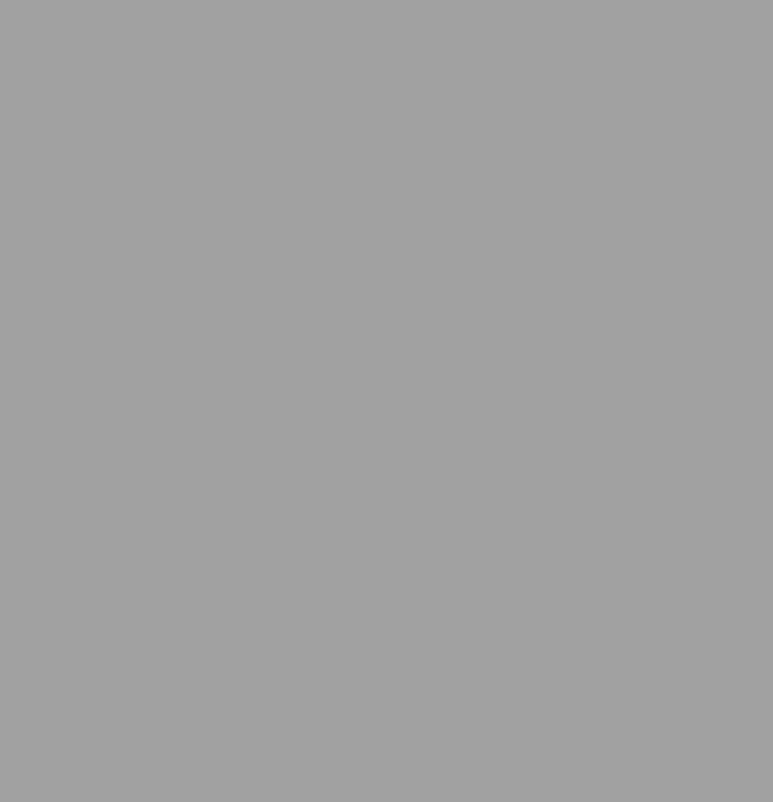
CompressionFit
TM
Governed by ASTM F3508, the CompressionFit HDPE pipe lining technology specifies an HDPE pipe with an outside diameter larger in size than the inside of the host pipe to be renewed. After the HDPE is butt fused to correspond to the pull distance, the pipe is pulled through a reduction die immediately before entering the host pipe. This reduces the HDPE pipe temporarily below the ID of the host pipe allowing it to be inserted.
While the towing load keeps the HDPE under tension during the pull, the pipe remains in its reduced size. The HDPE remains fully elastic throughout the reduction and installation process. After installation, the pulling load is removed. The HDPE pipe expands until it is halted by the inside diameter of the host pipe. The effectively natural ‘tight’ or ‘compression fit’ is accepted as exchanging an existing failing pipeline with a composite pipe in its place.
